Goodbye surprise malfunctions, hello predictive repairs
Sensors in our cars can already help prevent a crash before it happens, but what if they could also predict when to repair your car before a problem occurred?
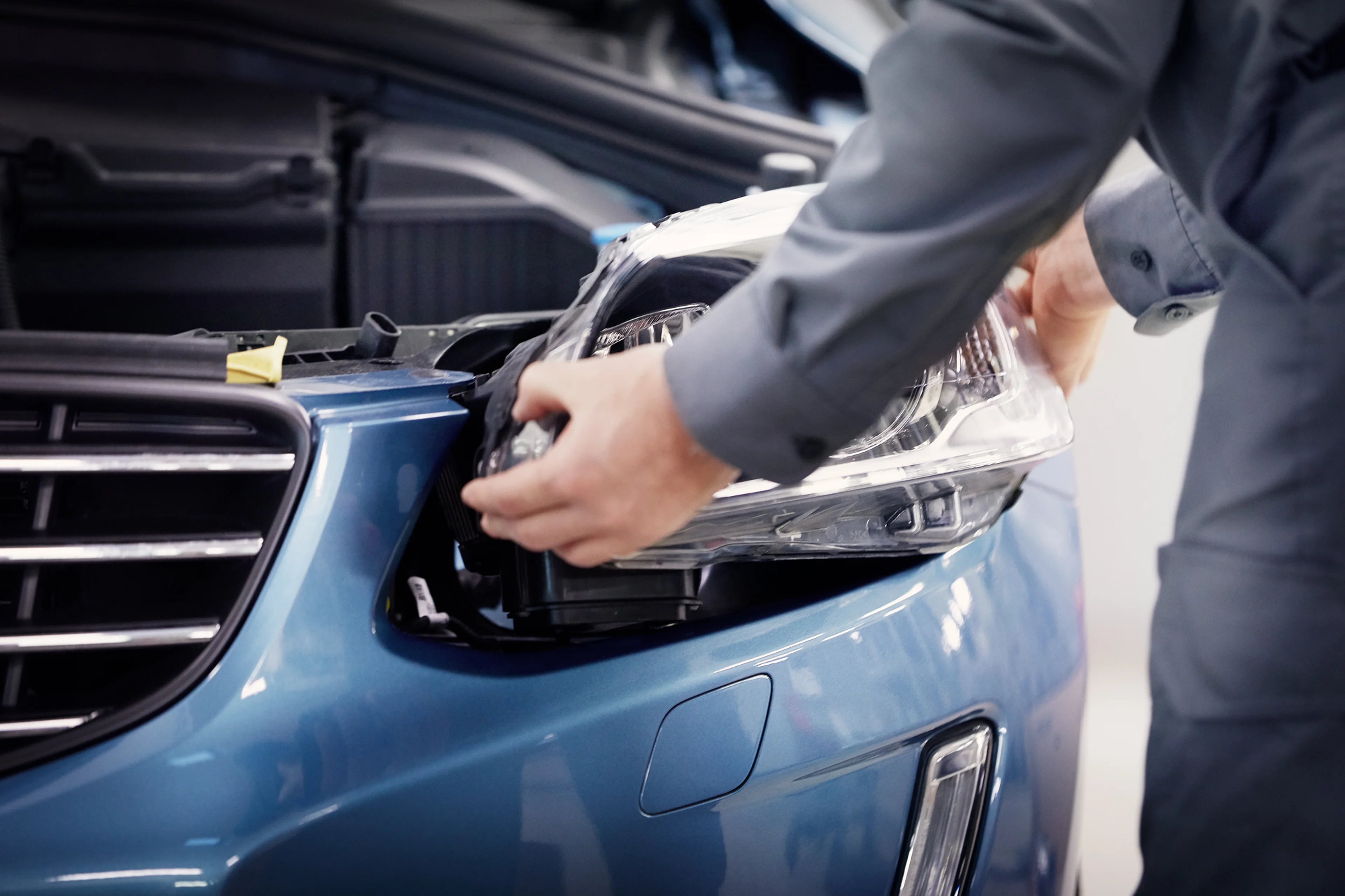
Can you foresee failures and fix them before they even take place?
Picture this: You’re parking your car after your morning commute when you get a call from your local Volvo service centre. Nothing feels out of the ordinary with your driving experience, but the service technician says that they have data indicating a potential problem and the car’s battery may need replacing. At your convenience, you’re asked to take the car to the workshop. While your car is being serviced, you get a replacement car to carry on with your life as usual. After the service is completed, you collect your car and drive off – unaffected by the battery failure that never happened.
This failure foresight may seem like something out of a sci-fi movie, but it’s really just a result of hard work carried out by the collaboration of several Volvo Cars teams*.
The core technology of this project, called the Remote Battery Monitoring System (RBMS), was created by data scientists Johnny Ngu and Herman Johnsson. Using this system we can collect, organise and use the massive amount of data emitting from each battery cell in our fully electric models.
“We have been collecting data for quite a long time, but it's like a hidden gold mine. You could say this is us finally making use of the data,” says Johnny Ngu. “The RBMS dashboard is just one application of the data we get from batteries; there can be other use cases such as predicting warranty coverage or even determining the level of aftermarket care our cars may need.”
Going from pure data collection into practical application in the company, project manager Cecilia Dano – accompanied by two graduates, Frida Zetterberg and Emma Åström –developed a way to assist customers directly.
Through the programme we gather data about the batteries in our cars, target potential battery issues and bring the car into the shop before the driver even experiences that something is wrong. All behind the scenes logistics are prepared by us beforehand so that the customer’s car is only at the workshop for one day compared to up to several weeks in the worst-case scenario.
We gather data about the batteries in our cars, target potential battery issues and bring the car into the shop before the driver even experiences that something is wrong.
This feature was recently launched in select cars offered from Volvo Bil Sörred in the Care by Volvo Co-Development programme. The technicians at Sörred used the data collected from the RBMS to develop and implement new working methods into an already complex process for this programme. Thanks to them, we have already replaced our first battery!
While the predictive repair features are currently available only with cars that have test equipment installed, there will be a full-scale pilot soon. The features will be offered to all Volvo and Polestar BEV owners in Norway that consent to sharing their battery data with us. Hopefully, this will be a start to eventually implementing predictive repair in all markets, so that customers never have to experience a surprise malfunction again.
“This programme can be a game-changer when it comes to the health of our fleet and the satisfaction of our customers,” says head of service operations Ana Erixon, whose team is responsible for providing an effortless car usage through an optimized service experience. “We know that some people still have hesitation around the batteries in electric cars, and we think that this programme will help alleviate some of those anxieties while also providing a personal touch to our customer service.”
Beyond the battery services being tested today, we might see this sixth sense being applied to other car components in the future. Theoretically, if we gather more information about specific car components, it would be possible to bundle the routine car service together with predictive and preventative repairs – saving the customer time while also efficiently fixing cars.
*This program has been carried out with teams from departments within Volvo Bil (service operations, customer service, business development and communications), central service operations (business development and battery centre), R&D, quality/warranty, procurement, and data protection.